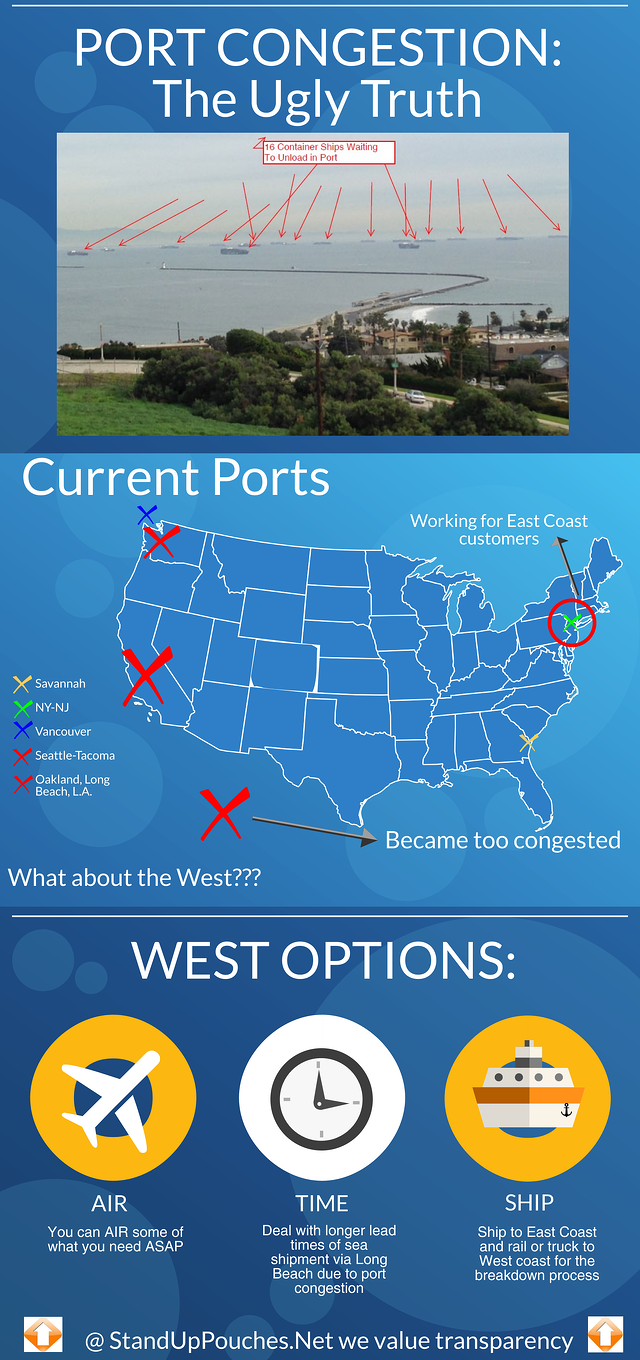
We’ve been in the retail packaging business for over 30 years and are fortunate to have survived many interesting situations that have affected our industry. These include oil shortages and drastic pricing spikes (oil is key ingredient for many types of retail packaging), fires and unexpected plant closures at massive resin manufacturers, Sept 11, trucking slowdowns and finally port strikes. They keys to survival is to have a plan and backup plans that you can rely on at a moment’s notice.
As leaders in the flexible retail packaging industry for items such as custom stand up bags and other types of barrier packaging, our clients count on us to guide them through any type of bump in the road and we are in the midst of one right now that we feel you should know about and prepare for.
To be clear, this information pertains to any company importing not just protective packaging but anything from overseas. As I mentioned earlier having a plan is the first step and then implementing it as needed.
What We Know:
- Summer of 2014 talk of a new contract between employers and the International Longshore and Warehouse Union (ILWU) in Long Beach-Los Angeles ports gets “hot” and employers suspend night shifts
- ILWU issues a slowdown and reduces crane operators from 110 per day to 35
- Contract negotiations get heated yet no official “strike” is issued (which means both sides will continue to talk)…(NOTE: normally this would be a good thing but the slowdown is worse than a strike as the US government would get involved with a strike…a slowdown they are staying out of it—at least so far)
- Backups (see picture) of container ships off the coast of Long Beach start happening.
- Sailings from Asia for All Products (not just retail packaging) is off by at least 3 weeks.
- Now ILWU is charging “additional fees” for unloading containers (think legal extortion)
What Happened Next:
- Since ships destined for Long Beach – Los Angeles cannot be re-routed once they arrive… they are forced to just sit there
- Delays and product spoilage is occurring for perishable products
- Containers are delayed 4-6 weeks resulting in canceled orders, lost revenue, insurance claims for spoiled items
- Many companies decided to ship to Seattle – Tacoma to avoid delays in Long Beach area (for new shipments, fyi)
- ILWU contacted Seattle-Tacoma union and “suggested” they slow down as well (should be severe penalties for this!)
Now:
- Ports of Long Beach and Los Angeles remain severely backed up
- Seattle-Tacoma ports are now backed up (overwhelmed with new containers + they have decided to use their leverage and slow down per ILWU suggestion)
What Are Your Options and What Should You Do (depends on where in US you are):
- East coast ports are NOT affiliated with ILWU. Consider shipping to New York-New Jersey or even Savannah, Georgia.
- Longer sailing time on the water 3-4 days but faster unloading and shipping
- Ship rail or truck as needed (even consider rail and truck back to West Coast)
- Air + Sea + Truck
- Ship what you absolutely need by AIR (not as expensive as you think) then ship the balance by Sea and add in extra time for congestion delays then by truck once it arrives (if you want to still ship via West Coast)
- Add 3-4 weeks to normal “lead time” and ship as you normally do (if shipping Sea to West Coast)
- Ship AIR (airport to airport)
- Many carriers (will ship full pallets by AIR)…very cost effective
- However you’ll need to arrange for pickup at the airport (Customs fees, duties, taxes, insurance, etc) (or have your logistics company arrange this)
- Buy from domestic supplier
- If this is even an option and this usually means higher per piece prices
- The right supplier will have these options as needed…but price and quality from overseas is still a great advantage.
- Count on your existing supplier! Order more than you need initially (a little forecasting ahead) and allow them to hold and release your product from their US warehouse. This IS Supply Chain in its truest form. Let your supplier hold your inventory and work off of your production requirements and deliver when and where you need it. Plan ahead and let your supplier help you. If they won’t help you (find a new supplier!)
What the unions and their employers are doing on the west coast (for allowing things to go this long and get this bad) is borderline criminal! At a time when our economy is showing signs of life again these two sides cannot find common ground…then they are charging exorbitant rates to do what they are supposed to do as part of their job (unload containers at a reasonable time)…something must change.
According to JOC.com, a leader in global intelligence for trade, transportation and logistics professionals, many companies are moving their sea freight to East coast ports and not coming back (of course until the East coast ports do something to screw up this golden goose). We applaud this action but know that sometimes this isn’t an option. Consider the information provided above for alternatives.
In closing, don’t try to handle these things by yourself. The retail packaging industry is littered with companies who have lost thousands of dollars and months of delays trying to “yell and make demands” on their suppliers in these situations (for example…if it isn’t here by next Tuesday I’m canceling the order). The purpose of this post is to hopefully shed light into what has and is happening with your imported products. This isn’t a supplier problem you are having (see picture of boats lined up at port of Long Beach) or even a logistics problem either. All of us are being screwed by the ILWU union and their employers. Move your products AWAY from these ports and hit them where it hurts…their wallets…and remind them when they come groveling back for work (you can be sure they will) why you left.